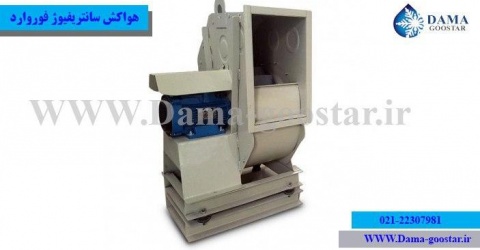
As you know, the Exhaust Fan is responsible for creating an induced flow in the air and moving the air from one point to another, and depending on its efficiency, it is divided into two general categories: blower and sucker. In industrial and domestic applications, where exhaust fans are used all over the world today, suction fans are mostly used for air exchange (hot air, unfavorable and toxic air). This means that the exhaust vent by the exhaust fan has a higher priority than the supply of fresh air by the supply fan.
Internal components of exhaust suction fan
To better understand the exhaust fan, it is better to take another look at the structure of the exhaust fan. The general structure of the exhaust fan produced by Damagester Company consists of different parts, which are:
- Electromotor: Motor is the driving force for the suction fan to rotate. At the request of the customer, Damagester Company uses domestically made electric motors (electrogen or motogen) as well as European brand motors such as Siemens or Russian for the exhaust fan of its production. The driving force or power consumption of the electromotor is selected for the exhaust fan suction based on the calculated volumetric flow rate of the air flow. The volumetric flow of induced air sucked by the Air Flow is expressed in cubic meters per hour (m3 / h) or cubic feet per minute (CFM). The electromotor of choice for exhaust fan suction has different types including synchronous and incynchronous and with different degree of protection (IP55 or IP54 or IP44) will be available.
- Blade Fan: Exhaust fan has forward, backward, radial and airfoil impeller which is designed and produced depending on the need for exhaust fan. The impeller causes air to flow inward by causing a local pressure drop in the exhaust fan
- Hosing: The main location of the impeller inside the exhaust fan is the housing or the so-called helical fan. A screw in the exhaust suction fan is responsible for collecting and directing the sucked air to the outside environment. The helical section is also responsible for securing the impeller against the entry of foreign objects into the exhaust fan.
- Coupling: This section is responsible for transferring power from the motor to the fan. The power transmission shaft in the exhaust fan is one of the important components because it transmits the generating driving force to the impeller. The transfer of electromotor output torque to the exhaust in suction fan exhaust is done in three ways. These three methods include direct connection, connection by money and connection belt with gearbox.
- Mechanical Seal: This part is responsible for maintaining the motor and power transmission shaft, and the use of this part will reduce the depreciation of fan and motor parts over time.
- Air inlet and outlet channel (Inlet @ Outlet Vent): This section is the main place of air inlet and outlet in the exhaust fan, which the use of circular sections greatly reduces the pressure drop and also reduces the noise produced in the exhaust fan. Be.
- Exhaust fan chassis: This part is where the exhaust fan is placed on the roof or other environment, which includes a chassis consisting of studs or H iron.
- Vibration damper or motor handle: One of the most important components that have a significant impact on reducing the level of sound produced by the device and reducing vibrations is the same vibration damper or so-called motor support handle that is used in residential environments (restaurants, buildings and offices) Highly recommended.
Exhaust fan classification based on user type
Suction fan exhaust is divided into ceiling (fungal), inter-channel, axial (centrifugal), centrifugal and utility categories in terms of efficiency. Axial fan and centrifugal fan in exhaust suction fan means which type of fan it works with. Each fan has its own characteristics and specifications. The centrifugal fan reduces the pressure and suction of the air by creating a centrifugal force in the exhaust of the suction fan, while the axial fan reduces the pressure and suction of the air by creating a turbulent flow in the exhaust of the suction fan. Exhaust fungal suction fan is installed on the roof and depending on the type of centrifuge or axial, it causes air to be sucked out of the building.
The argument we have always faced in air transfer in ducts is the drop in static air pressure per 10 meters of duct length. To solve this problem, we use an exhaust suction fan along the channel. It is also used because of the design and space constraints that can not be used with other exhaust fans. This type of suction fan is suitable for draining large amounts of moisture and heat.
When our desired location is such as hotels and tall buildings, instead of using a large number of exhaust fans, we use the integrated type, which has multiple inputs and also has high suction power, such as utility exhaust fans.
What is the reason for the loud noise generated in the exhaust fan and what is the solution to this issue?
Exhaust fan, like other air conditioning equipment, may sometimes cause a lot of noise and vibration due to non-compliance with production and installation standards. Exhaust fan can generally be installed in residential, office and commercial environments, depending on its type of use. And the loud noise generated by the exhaust fan can cause harassment to the residents of that area. The factors that cause noise and intensification of vibrations in the exhaust fan are as follows.
- Poor body Exhaust body Air exhaust fan
- Failure to comply with the principles on how to couple and transfer power from the engine to the impeller
- The type of blade or blade used in the exhaust fan impeller
- Fan rotation angle speed (fan speed)
- Inlet and outlet section of air suction and blowing duct (circular or rectangular)
There are different ways to prevent the problems of sound production and vibrations produced by the exhaust fan, and Damagaster Company is a leader in using these ways. Polymeric materials such as PVC or fiberglass FRP can be used in the production of the fan body to prevent the creation and intensification of vibrations in the body of the exhaust fan. In order to produce the body and assemble this device, instead of turning the edges together (bending the body sheets), they can be connected to each other by welding, which has a significant effect on reducing the vibration produced by the exhaust suction fan. In order to reduce the exhaust sound of the suction fan, our recommended solution is to use a fan box and a PLUG FAN.
Types of exhaust fan
As you know, the exhaust fan is classified into different types depending on the type of impeller and the model of blades used in it. In fact, based on the appearance of the type of blade and blade used in the impeller, exhaust fan is divided into the following types.
- Forward Exhaust Fan
- Backward Exhaust Fan Backward
- Radial Suction Exhaust Fan
- Exhaust fan Backward Airfoil
Forward impeller in exhaust suction fan
The forward centrifugal exhaust fan impeller has more blades than the backward fan fan impeller. The forward bent blades make much less noise than other blades. In this type of exhaust fan, the impeller blades have a forward curvature in the direction of rotation of the impeller.
Exhaust forward suction fan is used to move clean air due to its high sensitivity to solid particles suspended in the air. This type of exhaust fan has a low production noise and is also suitable for installation inside the environment. Due to having more blades than others, the forward exhaust fan has the problem of being consumed sooner. The efficiency of this type of exhaust fan is low and about 55 to 65. Forward exhaust fan is used to produce low flow and create low pressure drop.
Backward butterfly in exhaust fan
Exhaust fans of Beckward suction cups are cylindrical. The impeller blades are convex. Their curvature is opposite to the direction of rotation of the impeller. Smaller blowers have sloping blades that are not curved instead of convex blades. This type of exhaust fan is used to create air flow with higher speed and pressure. This type of exhaust fan has a higher efficiency compared to the forward and radial type. They are more economical for high energy applications than other types of exhaust fans.
Radial Exhaust Fan (Radial)
In this exhaust, the blade suction fans are straight and without curvature, and therefore they have the lowest sensitivity to dust compared to the rest of the suction fan exhausts. Radial blades produce the greatest static pressure drop, which significantly reduces the efficiency of the exhaust fan. This type of exhaust suction fan is used to move and transport particles. Radial exhaust fan is used for high pressure and low flow and also produces a lot of noise.
Exhaust fan Suction Beard Airfoil
This type of exhaust suction fan is the same type of backboard that has an airfoil-like blade. This exhaust fan has the highest efficiency and the lowest output noise. It is also used to produce high flow rates. This type of exhaust fan is not suitable for chemical and corrosive applications due to the low contact angle of the blade, and instead it should use a normal Beacon exhaust fan.