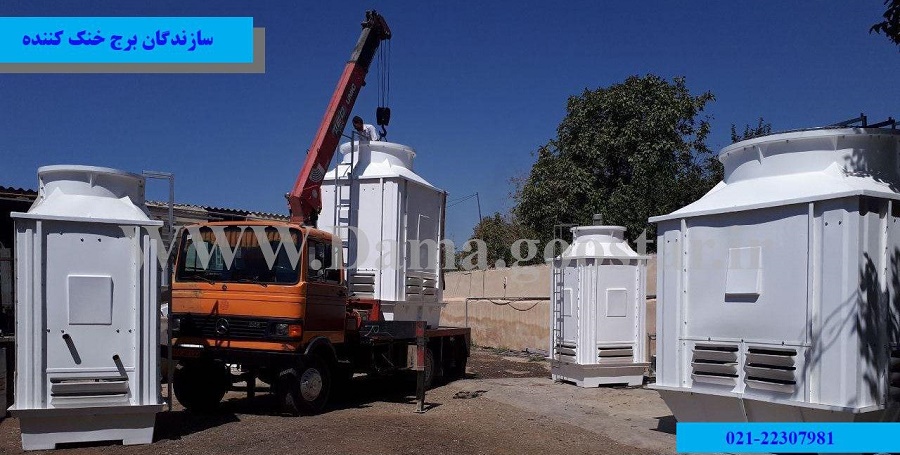
Manufacturers of cooling towers are naturally responsible for the construction and production of cooling towers and the main concern of this class is to improve the quality of cooling towers . To produce and supply with the latest and highest quality. The process of manufacturing and manufacturing industrial cooling products such as cooling towers is not possible except by relying on the knowledge of fluid engineering, chemical engineering and electrical engineering.
The daily advancement of engineering knowledge in the field of cooling and heating installations has caused the manufacturers of cooling towers to seek to upgrade and optimize their products. Manufacturers of cooling towers in order to advance their goals in production and construction today with the participation of academic and engineering knowledge and also with the cooperation of consulting companies such as Sazeh Company are looking for solutions to improve the quality, automation of production and energy efficiency of their products.
The builders of cooling towers around the world have always gathered annually and monthly in different seasons, and with their consensus and mental participation, they have created new and dynamic ideas in the cooling and power production industry. The world's leading manufacturers of cooling towers are Evapco-Marely-CTS-CTI-EBARA-SPX-Paharpour, which are pioneers in the field of science production in the global refrigeration industry. In fact, it depends on the field of activity of the world's reputable companies in the field of construction and production of cooling towers. This equipment is offered in the form of international (international) production and domestic production and production.
Learn more: Cooling tower
International cooling tower builders
Marley America is a leader in the manufacturing industry of cooling towers and accessories. The company has been operating in the United States since 1970, and today one of its most prestigious products, the two-cell cooling tower, nicknamed the Marley Design, is being designed and manufactured around the world.
The largest manufacturer of cooling towers in the world is CTI Company, which provides global and international standards to other countries and manufacturers of this product in the production and construction of cooling towers. Today, many manufacturers of cooling towers are seeking to obtain a valid production license certificate from CTI in the field of cooling tower, and so far 4 companies in Iran have succeeded in obtaining this license in their products.
Oapco is of American origin and has been operating in the North American continent since 1976. It is now the father of the world's air conditioning industry and is one of the world's leading manufacturers of galvanized cooling towers. Today, OPEC, with more than 56 branches in various countries, is the largest producer and exporter of cooling towers.
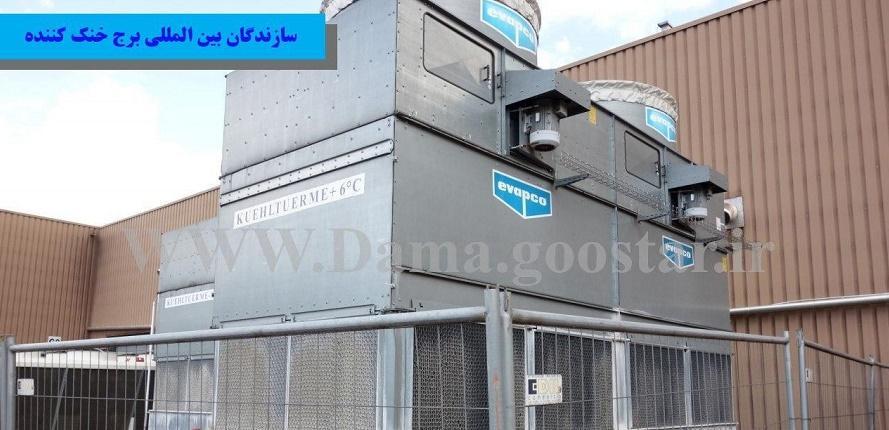
The company is headquartered in Central Asia and has started operations in Japan for the first time. The most famous reason for the reputation of this reputable brand is the production of cooling towers for the production of one of the most common and best examples of cross-flowing cross-flowing coolers called crossovers or Abara cooling towers. This special model of various types of cross-flow coolers with the highest production and manufacturing circulation has been offered in this company.
The company is of American nature and manufactures, designs, manufactures and supplies a variety of industrial cooling towers in the oil-rich Gulf states, including Iraq, Saudi Arabia, Kuwait, Egypt and Qatar, which has been in operation since 1995. In 2008 he moved to the United Arab Emirates.
The company, like many reputable companies in the field of manufacturing and production of cooling power in the United States, started in 1998, and for the first time, the design of a multi-purpose cooling tower in this company has been conceived.
CTS is one of the most reputable manufacturers in the Middle East. It has been awarded the ISO 9001, ISO 18001 mark and various and valid standards by the American company CTI.
Manufacturers of cooling towers in Iran
Dam Gostar Company has been operating in Mashhad since 2001 and after a short period of time, it has moved to Tehran and today it is considered the founder and innovative idea in the construction of low-consumption hybrid cooling towers. Today, with the aim of improving the quality of its products, the company has 16 cooling and power models for productivity in different climatic regions. Today, all types of cooling devices produced by Dam Gostar Company are supervised by the best quality control team (QC) and are provided to the general public.
Parto Abgardger Company has started its work with the holy city of Mashhad in the production and construction of circular or conical cooling towers and today it is operating throughout Iran under the name of Tochal Ventilation of Iranians. The company is one of the most reputable and oldest manufacturers and manufacturers of cooling towers.
Aria Beniz Company is one of the most reputable and largest manufacturers of cooling towers in Iran, which uses the knowledge of engineering to boldly be one of the top design teams for cooling and power. Ariabnews is also currently exporting to foreign countries.
Mahtab Gostar Company is one of the most reputable engineering companies in the field of air conditioning systems, especially the production and construction of cooling towers, which has 6 reputable and active branches throughout Iran to provide after-sales services.
Nab Zist Co. is one of the top manufacturers of cooling towers in Greater Tehran and throughout Iran, and today, by producing multi-cell cooling towers, it promotes and controls the energy consumption of the cooling tower.
The main concerns of the interior builders of the cooling tower
- Preparation of quality raw materials for proper and standard production of products
- Lack of proper and standard equipment in the production line of parts and accessories for cooling tower
- Customer dissatisfaction due to the existence of many intermediaries in the sales market
- Lack of economic justification for after-sales service
- The counterfeiting and poor quality of the parts and materials used in the manufacturing process, which reduces the final quality of the product.
- Manpower inefficiency in the production sector and non-compensation of this issue by automating production due to lack of parts production equipment (due to economic sanctions)
- Design and production of cooling towers by non-specialist builders, which has led to a loss of confidence in national production and dissatisfaction of other industrial classes with the support of domestic manufacturers.
- Reducing the cost of some manufacturers and builders of cooling towers and increasing customer dissatisfaction after purchasing a cooling tower creates the attitude of reducing the cost by reducing the quality of materials by other manufacturers.
Construction and production of cooling towers
The process of building or building a cooling tower includes various parts of different parts of the construction of parts and assembling them in the cooling tower. In other words, the process of production and construction of the cooling tower is divided into three main parts. The first part involves the production of cooling tower components and the second part is related to the assembly operation, and the final part is the technical and engineering supervision (quality control).
The process of building a cooling tower must be done with great care, as this results in valuing and valuing the final quality of the equipment produced. The cooling tower has various equipments related to water supply and water supply parts and has different parts that are produced from metal, polymer or fiberglass FRP material. Most manufacturers today are trying to limit the use of metal materials in the production of interior parts of cooling towers and use high-strength materials such as fiberglass or polypropylene instead.
Due to the above, the manufacturers of cooling towers in the production and construction of cooling towers may deal with different parts of production. In fact, building a cooling tower requires technical knowledge in the field of fluid, chemical, electrical, civil and materials engineering. Electric motor is one of the parts related to electrical engineering. Therefore, a successful manufacturer in the construction of cooling towers must have a complete and experienced team of engineers in various fields.
The general steps of building a cooling tower by domestic builders
1- Manufacture of parts and accessories used in different parts such as impeller, nozzle, packing, drip trap and body components
2- Assembly and assembly of parts and equipment on the main body and frame
3- Quality control and technical supervision of the produced product in accordance with various standards and tests, including dewatering test, welding test and pressure test.
Various parts for making cooling tower parts (before assembly)
- Injection of plastic and polymer parts such as nozzle or spray nozzle, drip trap and packing media
- Shaving of metal parts from steel and aluminum materials such as round reduction (Foley) and Sprinkler (water turbine)
- Production of body parts from FRP fiberglass material with fibers and resin and using molding and manual or machine baking method
- Coil chassis welding, drip and pack holder support, fan guard or butterfly guard and butterfly and motor holder chassis at the top of the fan neck
- Construction and production of butterfly blades or cooling tower fans using extruder or hydraulic press and assembling that part is machined with the hub part and then going through the steps of static and dynamic balance of the impeller.

Cooling tower assembly
The process of assembling or finalizing a product involves placing different parts in the intended parts. In fact, the next step in supplying and producing the side components of a cooling tower is the assembly or heading of the cooling tower. This step can be done in two ways according to the necessary qualifications for transportation and installation.
- Assembly at the project site (cooling tower installation site)
- Assembly in the factory or workshop for the manufacture and production of cooling towers
Depending on the capacity and dimensions of the cooling tower, the process of assembling or building a cooling tower can be done in both cases. Generally, capacities of more than 500 tons of refrigeration in the cooling tower are assembled at the project site. Sometimes for various reasons, many manufacturers try to assemble all their products in the form of assembly and delivery to the factory door. Due to this purpose, capacities above 500 tons of refrigeration, which will be very difficult to transport and load, will be designed and produced in multi-cell.
Reasons why construction companies refuse to assemble and build cooling towers at the project site
- Lack of quality control of the technical supervision team correctly and efficiently due to the possible length of the distance
- Decreased product quality due to fatigue due to distance and assembly time on executive and assembly personnel
- Increase production time, construction, installation of cooling towers
- Increase in transportation costs, food, accommodation and staff assembly operations
Partial steps to build a cooling tower
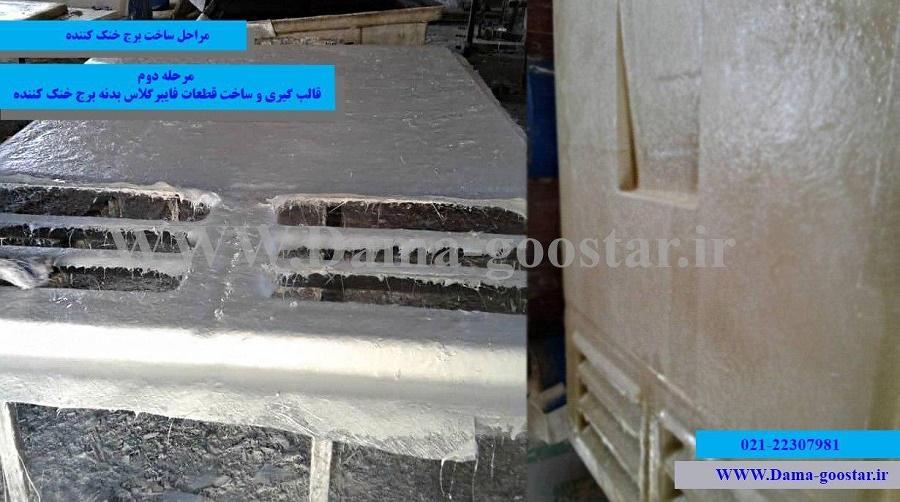
- 1- The stage of production and payment of initial molds of fiberglass body parts
- 2- The process of molding and making fiberglass parts of the cooling tower from the mother mold
- 3- The cooking stage of fiberglass parts in front of the sun or furnace baths
- 4- Fiberglass body parts payment step with milling and polishing machine in order to polish and eliminate appearance defects in manufactured parts.
- 5- Granule material injection stage in plastic injection machines for making and producing plastic parts such as nozzles, drip trays and cooling tower packing
- 6- Shaving metal parts such as round reduction system, sprinkler, inlet and outlet flanches and hubs and impeller and fan handles
- 7- Extrusion of fan blades with fiberglass or aluminum material with airfoam cross section (Airfoil)
- 8- Cutting and welding of parts for fan, motor and power transmission system and internal parts support systems.
- 9- Glazing of metal parts such as coil support (in CCTV cooling towers), drip support, packing, pipe and nozzle
- 10. Assembly and assembly and final construction of the main body of the cooling tower consisting of fan deck, beacon (panel), panel, column and louvers
- 11- Placement and installation of side parts made in the cooling tower
- 12- Installing and tightening the belts of the power transmission section
- 13- Sealing fiberglass seams in different parts of the body and water inlet and outlet flanches
- 14- Drainage test, welding test (for coil), pressure test (for water and coil inlet pipes)
- 15. Final monitoring of the technical supervisor of Demgostar Company and elimination of possible defects caused by human errors in the production and construction of cooling towers.