سیستم انتقال قدرت یا کاهنده دور موتور در برج خنک کن وظیفه کاهش سرعت چرخش شافت دینام را برعهده دارد. شافت دینام با اتصال به فولی سر پروانه دور خروجی اش کاهش پیدا می کند و سرعت چرخش پروانه نیز کاهش می یابد. کاهنده دور در برج خنک کننده همانند یک قطعه ای است در کاهش دادن سرعت چرخشی فن . فن یا پروانه اگر با سرعت زیادی گردش کند کولینگ تاور به دلیل مکش بیش از حد هوا سبب آسیب به قطعات داخلی می شود. در اصل هر پروانه متناسب با قطر و میزان هوادهی ایجاد شده نیازمند یک میزان سرعت چرخش معین است. موتور به صورت تسمه ای یا گیربکسی یا به صورت درایو مستقیم به فن یا پروانه اتصال می یابد. در واقع تسمه پولی و یا گیبرکسهای متصل شده به دینام سبب کاهش دور موتور در خروجی به فن می شود. در ظرفیت های پایین برج خنک کن از سیستم کوپل مستقیم جهت انتقال قدرت از دینام به موتور استفاده می شود. دور موتورهای صنعتی نصب شده در برج خنک کننده در این نوع سیستم انتقالی قالباً 700 یا 900 دور بر دقیقه است. در سیستم های انتقالی گیربکسی به دلیل کاهش دادن مصرف انرژی و آمپر مصرفی کولینگ تاور از موتور با دورهای بالا استفاده می شود. در سیستم های گیربکسی یا تسمه ای از موتورهای 1450 و 2900 دور بردقیقه جهت چرخش پروانه استفاده می شود. بیشترین کاربرد انتقال حرارت گیربکسی در برجهای خنک کننده صنعتی و نیروگاهی بوده که بدلیل اهمیت سیستم پاره شدن تسمه معضل بزرگی به شمار می آید . بیشتر شرکتها و کارخانجات صنعتی از گیبرکسهای هلیکال جهت انتقال قدرت در برج خنک کننده استفاده می نمایند. 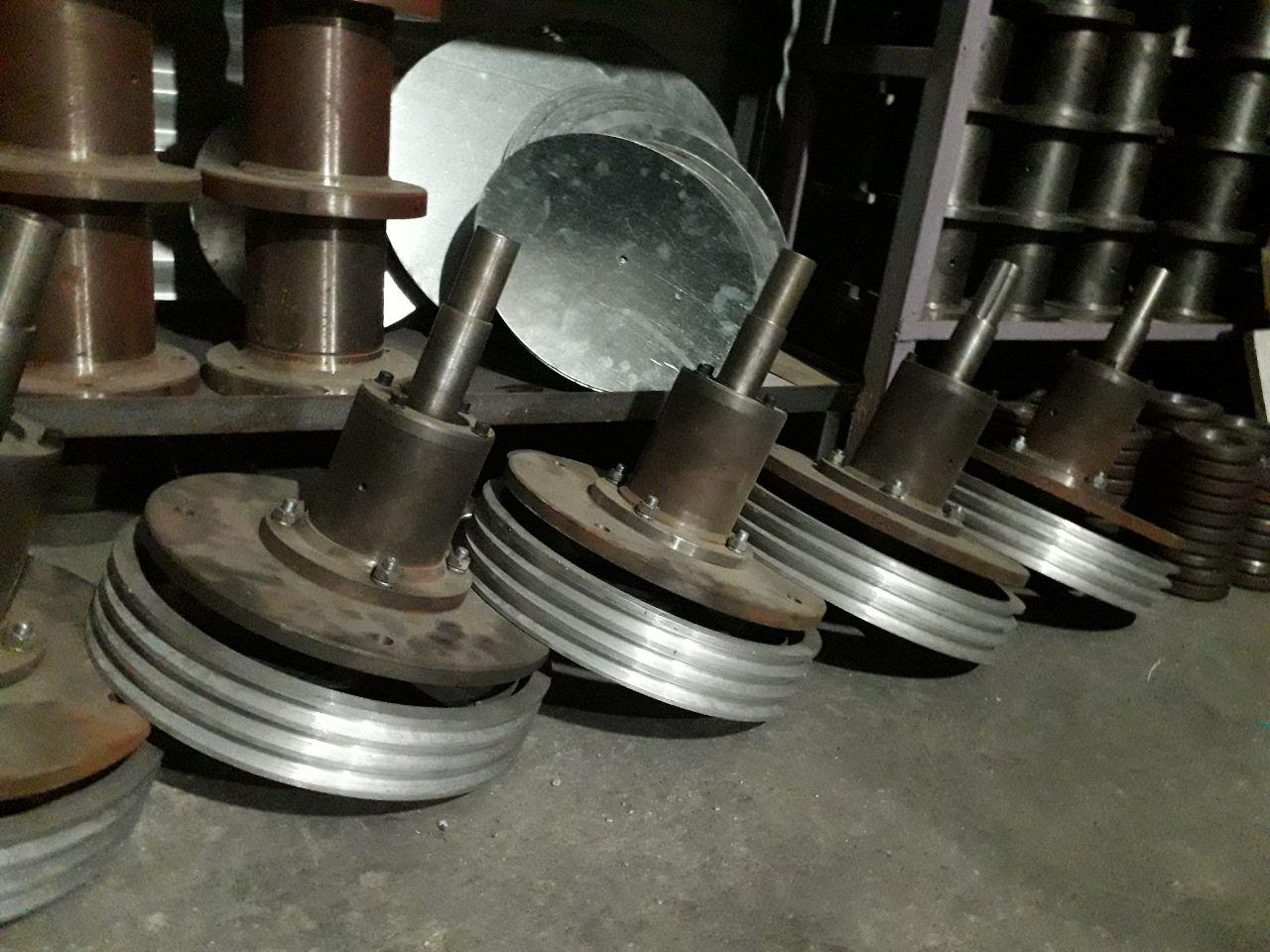
انتقال قدرت گیبرکسی در برج خنک کننده
گیربکس ها می تواند به صورت شافت مستقیم یا هلیکال و یا به صورت گیبرکس 90 درجه ای به موتور متصل می شوند. گاهی اوقات شرکت سازنده موتور گیبرکس را به موتور متصل می کند و به صورت کوپله مستقیم تحت عنوان الکتروگیربکس ارائه می دهد. در واقع الکتروگیربکس در برج خنک کننده ترکیبی از گیبرکس دنده ای شفت مستقیم با دینام دور بالا می باشد. الکتروگیبرکس ها علاوه بر شاخصه توان دارای مشخصه دیگری تحت عنوان دور خروجی می باشند. دور خروجی گیبرکس در واقع ورودی به هاب فن بوده که سبب چرخش پروانه با دور استاندارد می شود. گیبرکسها از حساسیت بیشتری در تعمیر و نگهداری برخوردارند. مهم ترین بخش نگهداری برجهای خنک کننده با سیستم انتقال قدرت گیبرکس در روغنکاری منظم بلبرینگ ها و دنده های داخلی این قطعه می باشد. روغنکاری منظم گیبرکس همانند تعویض روغن ماشین تاثیر بسیاری در عمر و نحوه کارکرد این قطعه می گذارد. جهت روغنکاری گیبرکس برج خنک کننده از انواع گیریس نسوز می توان استفاده نمود. به دلیل چرخش دائمی شافت و محور چرخش دینام این قطعه دائماً در نقطه دنده تحت اصطکاک قرار دارد. به دلیل اصطکاک زیاد بین دو چرخ دنده در داخل گیبرکس از روغن جهت روانکاری استفاده می شود. مهمترین ویژگی روغن یا گریس در روانکاری چرخ دنده ها داشتن مقاومت دمایی بسیار بالا در مقابل تنشهای حرارتی است. به دلیل فوق در سیستم روغنکاری سیستم کاهش دور برج خنک کننده(گیبرکس) بکارگیری گریس نسوز (با مقاومت دمایی بالا) توصیه می شود.
انتقال قدرت تسمه ای در برج خنک کننده
انتقال دور یا قدرت از موتور به دینام در اکثر موارد به دلیل راحتی کار و اقتصادی بودن نوع تسمه ای می باشد. انتقال قدرت تسمه ای در برج خنک کننده شامل بخش فولی سر پروانه ، فولی سر موتور و تسمه می باشد. تسمه با قابلیت ارتجاعی خود نیروی دورانی فولی موتور را به پروانه انتقال می دهد. این انتقال گشتاور گاه با ضرباتی همراه است که تسمه برج خنک کننده با داشتن قابلیت ارتجاع این ضربات را دفع می کند. تسمه های بکار رفته در سیستم انتقال قدرت برج خنک کننده از نوع باریک در سایزهای گرید A و B می باشد. اندازه تسمه که تحت عنوان یک عدد در کنار حروف انگلیسی بیان میشود در واقع نصف محیط تسمه در حالت آزاد است. بخش فولی سر پروانه خود از قسمتهای مختلفی تشکیل میشود. بلبرینگ کف گرد ، شافت انتقال قدرت و پولی تسمه خور قسمتهای اصلی کاهش دور برج خنک کننده است. بلبرینگ های ساچمه ای گردش محور دوار را از طریق شافت به هاب فن منتقل می کنند. شافت حد واصل بلبرینگ ، پولی با هاب یا قسمت مرکزی فن می باشد. هاب با اتصال به تیغه های پروانه سبب چرخش تیغه ها با سرعت چرخشی معین می شود. تسمه پولی برج خنک کننده با متریال چدن ریخته گری یا آلومینیوم تراشکاری تولید می شوند. آلومینیوم به دلیل نرم بودن عموماً پس از یک مدت هرز می شود و یا از نقاط کلیدی دچار برش می شود. نیروهای برشی در مقطع اتصالات در کاهش دور برج خنک کننده به شدت زیاد بوده و این موضوع مستلزم استفاده از متریال با کیفیت ایده آل است.
مطالب مشابه :