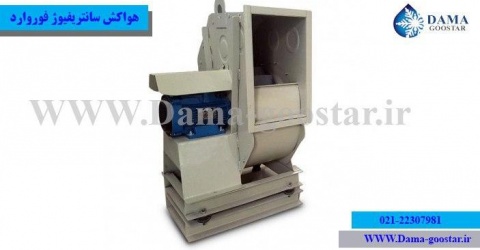
Commissioning or operation of the cooling tower is the last step in using the cooling tower in the design of the cooling tower system. Operation is the final step in selecting a cooling tower that has high sensitivities. The correct operation of the cooling tower is in fact the result of the correct selection and installation of the cooling tower. After completing the installation of the cooling tower, it is necessary to set up the cooling tower and put it into service. The operation of the condenser water system of a heating device such as a chiller or boiler consists of several basic and mandatory parts. In the most important part of designing and operating the condenser system is the cooling tower. The placement and installation of condenser cold water cycle accessories has a significant impact on the output. In fact, the correct operation of the cooling tower is a function of the correct installation of the cooling tower and accessories.
The effect of observing safety issues in setting up a cooling tower !!
Observing the safety points and checking the peripheral equipment in connection with the cooling tower is one of the most important principles of using the cooling tower. In fact, before turning on the cooling tower and starting the condenser system, we must make sure that each equipment is working properly. Proper operation of industrial cooling and air conditioning system has many benefits. Failure to follow the principles in the setup operation may cause damage to the main parts of the devices.
Observing the basic points in the initial start and checking the important items can have a great impact on the basic operation of the cooling tower . The commissioning of an industrial or refrigeration equipment is done correctly when the least amount of error is made in it. Reducing the incidence of errors in the commissioning process by an expert should be done in accordance with the principles of operation of the cooling tower.
Basic principles in setting up a cooling tower
How to properly install peripherals such as pumps, cold water tanks, hardeners, etc.
Proper arrangement and proper placement of equipment in the condenser cycle
Use of protective equipment in the control panel to protect fan and pump motors against human errors
Use of cold water flow regulating valves in the piping circuit between the cooling tower and industrial devices
Use of shock absorbers in the piping circuit and in the main chassis holding the main equipment
Temporary start-up of the system (in the form of a starter) and fixing possible problems
Check and re-inspect the checklist by the relevant expert
Observe safety tips and setup requirements in accordance with the installation manual provided by the manufacturer
Final commissioning of the system and long-term operation of the equipment and elimination of possible defects
The main components to be controlled before starting the cooling tower cooling system
cooling tower
Cold water storage tank
Cool water circulator pump
Pipes and fittings (side valves of circulating water circuit)
Exothermic device (chiller or industrial device)
Circulating water treatment equipment (hardeners or micron filters or RO package)
Control items in the correct installation of the pump in the process of setting up the cooling tower
Pump installation control includes mounting the pump, connectors, vibrators and plumbing fixtures such as valves, filters, pressure gauges, thermometers, etc.
Axis control (pump shaft and its coupling alignment
Lubrication or pump shaft arches according to the manufacturer's instructions
Lubrication of motor shaft bearings according to the manufacturer's instructions
Rotate the shaft by hand to ensure free rotation of the pump motor
Control of the correct direction of rotation of the electric pump shaft with blade starter
Controls in the water treatment system in the cooling tower condenser circuit
Control of pH sensor catheters or rods and navigability for proper installation
Test the performance of the solenoid valve to drain or adjust the flow of water or underwater
Putting water purification equipment in operation
Final control items before setting up the cooling tower
Cleaning the tower surfaces, washing and cleaning the upper pan and the lower mattress of the tower
Cleaning the smoothness of the lower pan of the tower
Lubrication of fan shaft bearings according to the manufacturer's instructions
Lubrication of motor shaft bearings according to the manufacturer's instructions
Test and adjust the thrust drive (if installed)
Adjusting belt tension (s)
Control and adjust the alignment of the belts
Control of alignment of motor pulley shaft with impeller pulley
Control the couplings for tightening the screws, not playing them, etc.
Rotate the fan or impeller shaft by hand to ensure that the fan and bearings rotate freely
Control the correct direction of rotation of the fan or impeller shaft with a blade starter
Short-term fan start and control of noise and vibration
Drain and rinse the condenser water pipes with water and then chemicals
Fill the lower pan and tower and condenser pipes with water according to the manufacturer's instructions to the required amount
Short-term rotation of condenser pump and fan motor according to correct installation principles
Placement of fan motor amp and pump alternator in nominal plate values
Test the correct distribution of water in the nozzles or upper pan, inner plates and lower pan of the cooling tower
Vortex flow control of the lower pan of the cooling tower
Test the thermostat and heater system for frost protection
Condenser water balance of each cell in terms of reciprocating current in multicellular systems
Testing the water level controls of the lower pan of the tower, including low and high limit warnings and checking the floating function
Control the correct installation of temperature sensors
Test the performance of the bypass control valve and adjust its 70-degree rotation
Check the correct operation of fan control relays
Proper VFD performance test (if installed)
Check the function of the vibration switch
What is the importance of setting up a cooling tower in principle?
Perhaps asking this question will help a lot in learning the above as much as possible. In answer to this question, it should be stated that the cooling tower or cooling tower is a fully advanced device consisting of electrical and mechanical components. The main components of the cooling tower should actually have its proper and optimal performance when starting up. If one of the parts does not work properly at the beginning of the commissioning process of this equipment and the refrigeration machine, its complications will soon cause damage to other parts. In fact, by correcting the errors in the installation process of the cooling tower before commissioning, irreparable damage can be prevented. In fact, the start-up operation is the last chance to fix possible errors in production or installation. Common errors such as incorrect adjustment of the cooling tower impeller angles or incorrect threading of the nozzle on the clamp will be easily noticeable at this stage.
The main benefits of setting up a cooling tower correctly
- Proper operation of the cooling tower with the highest possible efficiency
- Correct and optimal use of cold water to cool the chiller
- Optimal operation of industrial devices connected to the cooling tower
- Increase the life of the internal components of the device
- No possible damage to other parts due to a defective part
- Reduce financial losses due to possible mistakes during production
- Reduction of casualties due to possible dangers of not operating the cooling tower properly